FIBERGLASS VS. ALUMINUM BOATS - WHICH IS BETTER?
By: The Salish Seaman
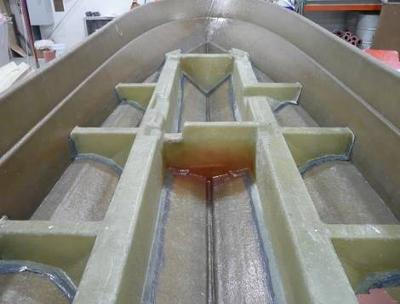
The two most common materials used in modern small vessel construction are aluminum and fiberglass. Like most things in life, each has their pros and cons.
Let’s first look at the traditional and most common - molded fiberglass. A FG boat is built literally from the outside in. After the female mold is prepped, the very first thing that is applied to it is the ‘paint’ colour in the form of gelcoat. Once that cures then the structure/strength of the hull is built inwards. On more price point boats the common method of applying the FG strand and resin is via a ‘chopper gun’. This is the quickest thus the cheapest way of laminating a hull. The applicator is called a chopper gun because it literally take a long continuous strand ( think string ) of fiberglass, then inside the applicator gun, it chops the strand into small pieces, mixes it with the resin, and sprays the resin soaked short pieces of FG stand into the hull. So the advantage is….fast thus inexpensive. The disadvantage is all the little short pieces lack the structural strength of using FG mat ( hand laid ) and the potential exists for inconsistent lamination thickness ( thus inconsistent strength ).
Now compare this compilation of thousands of short pieces of FG to a large sheet of manufactured 2 or 3 dimensional FG weave. Just like in other textile manufacturing, the woven mat is manufactured to very precise and controlled thicknesses and strengths. When a boat is hand laid, the manufacturer is in complete and accurate control of how heavy (strong) the mat is and if they require stronger areas in a particular parts of the hull they simply build up additional layers of resin saturated mat. Some high end manufacturers are using the latest technology in 3 dimensional weave mats which gives the added bonus of getting the required thickness ( strength) in one layer of mat without having to resort to multiple layers which have a potential risk of delamination in an impact ( have you ever had a pair of snow skis delaminate? ). Hi- tech and super strong materials such as Kevlar can also be used by high end builders who place more of a priority on hull strength than they do cost.
So after 2 paragraphs of FG hull lamination 101, the summary is that a good strong FG hull will be heavier than a more lightly laminated hull…not rocket science. Before the big answer you have patiently been waiting for I suppose I should touch on how aluminum boats are built.
Aluminum boats tend to fall into 2 broad categories. Most smaller and price-point boats are made from slightly overlapping panels of relatively thin aluminum, these overlaps are then riveted together with a sealant between the panel joints. Then some internal trusses or braces are riveted into place for strengthening since the thin aluminum will flex so much. Boats like this tend to be best used in more gentle environments such as lakes and rivers. If subjected to more extreme conditions the thin aluminum can over time flex to the point of fatigue (cracking) as well as the rivets and joints will flex, stretch and ultimately leak water. Also moisture can sit in these compromised joints and cause corrosion, especially in the salt water environment.
More heavy-duty purposed boats will be made from a thicker (heavy gauge) aluminum and the joints welded. . Thicker means stronger, and a good weld is as strong if not stronger than the surrounding material which is evidenced by the lifetime hull warranties offered by the best builders. Some builders shape their hulls rather free form while with some others the aluminum sheets are forced into bends around an internal steel jig to shape the hull and then the panels are welded into place. A straight piece of aluminum sheet can flex under sufficient wave pressure. This flex, often referred to as oil-canning, can contribute to the noise often associated with aluminum hulls (topic covered below). By forcing the aluminum into an engineered bend around a jig, the material is put under tension which both increases its strength and takes away ‘oil-canning’. This is simple to see for yourself: take a business card gently between your thumb and forefinger and with your other forefinger poke it in the middle to see how easily it flexes. Now increase your grip pressure a bit so that the business card flexes slightly outwards, now poke it again, no flex, voila , you just engineered a stronger and quieter business card!.
Key attributes of aluminum are being both strong AND lightweight so in a nutshell a heavy gauge welded aluminum hull will be very strong in a lighter package than a comparably strong FG boat hull. End of story? Of course not!
We can all appreciate the safety, ruggedness, and long lifespan that a strong boat offers. But do we want light-strong or heavy-strong?
Light = less displacement = rides higher in the water. An advantage to this is we can get by with less horsepower and fuel to move the boat. Pretty much all will agree lower fuel consumption is very attractive. However these same attributes that make the boat easier to push tend to make the boat get ‘bounced around’ a bit more as wind and waves will have a greater effect on a lighter boat. In contrast to this the heavier FG boat all other things being equal will be more ‘look out waves I’m coming through’, just remember it will need more power and fuel to accomplish this.
Another popular attribute of aluminum is abrasion resistance, so if you want to beach your boat regularly, whether boat camping, unloading people and gear at the cabin, or going ashore for a hike or to get clams or oysters, the durable abrasion resistant aluminum is ideal.
Detractors of aluminum boats point out that they are noisy and in comparison they will tend to be more so than FG. Metal tends to transfer vibration, which can be heard as noise, while fiberglass absorbs vibration. We’ve all sat on the top deck of a BC Ferry and noticed that. In reality though both FG and aluminum pleasure craft hulls are foamed filled both for Coast Guard flotation and sound/temperature insulation. In an open boat ambient wind noise easily masks any hull noise but in my experience in a full cabin boat I will say hull noise is a bit more noticeable from an aluminum hull compared to a fiberglass hull.
Fiberglass boats will have the aesthetic advantage of having better visual looks and hull shapes. Since the material is molded, more advanced and attractive shapes can be made. Aluminum construction on the other hand is made from cutting, bending and welding large sheets of aluminum and various other aluminum angles and extrusions, thus an aluminum boat will tend to be a bit more basic/angular/industrial looking. Beauty is of course in the eye of the beholder.
So the answer is?? Of course there is no definitive answer which is why both types of boats remain so popular (remember those cement sailboats?!). If you want an attractive and sporty runabout for the lake, or a luxury cruiser, the aesthetics of fiberglass will probably push that boat to the top of your wish list. And if you own a pickup truck and value utility over flare I see a heavy gauge welded aluminum boat in your future.
SEE MORE BOAT BLOGS HERE
Let’s first look at the traditional and most common - molded fiberglass. A FG boat is built literally from the outside in. After the female mold is prepped, the very first thing that is applied to it is the ‘paint’ colour in the form of gelcoat. Once that cures then the structure/strength of the hull is built inwards. On more price point boats the common method of applying the FG strand and resin is via a ‘chopper gun’. This is the quickest thus the cheapest way of laminating a hull. The applicator is called a chopper gun because it literally take a long continuous strand ( think string ) of fiberglass, then inside the applicator gun, it chops the strand into small pieces, mixes it with the resin, and sprays the resin soaked short pieces of FG stand into the hull. So the advantage is….fast thus inexpensive. The disadvantage is all the little short pieces lack the structural strength of using FG mat ( hand laid ) and the potential exists for inconsistent lamination thickness ( thus inconsistent strength ).
Now compare this compilation of thousands of short pieces of FG to a large sheet of manufactured 2 or 3 dimensional FG weave. Just like in other textile manufacturing, the woven mat is manufactured to very precise and controlled thicknesses and strengths. When a boat is hand laid, the manufacturer is in complete and accurate control of how heavy (strong) the mat is and if they require stronger areas in a particular parts of the hull they simply build up additional layers of resin saturated mat. Some high end manufacturers are using the latest technology in 3 dimensional weave mats which gives the added bonus of getting the required thickness ( strength) in one layer of mat without having to resort to multiple layers which have a potential risk of delamination in an impact ( have you ever had a pair of snow skis delaminate? ). Hi- tech and super strong materials such as Kevlar can also be used by high end builders who place more of a priority on hull strength than they do cost.
So after 2 paragraphs of FG hull lamination 101, the summary is that a good strong FG hull will be heavier than a more lightly laminated hull…not rocket science. Before the big answer you have patiently been waiting for I suppose I should touch on how aluminum boats are built.
Aluminum boats tend to fall into 2 broad categories. Most smaller and price-point boats are made from slightly overlapping panels of relatively thin aluminum, these overlaps are then riveted together with a sealant between the panel joints. Then some internal trusses or braces are riveted into place for strengthening since the thin aluminum will flex so much. Boats like this tend to be best used in more gentle environments such as lakes and rivers. If subjected to more extreme conditions the thin aluminum can over time flex to the point of fatigue (cracking) as well as the rivets and joints will flex, stretch and ultimately leak water. Also moisture can sit in these compromised joints and cause corrosion, especially in the salt water environment.
More heavy-duty purposed boats will be made from a thicker (heavy gauge) aluminum and the joints welded. . Thicker means stronger, and a good weld is as strong if not stronger than the surrounding material which is evidenced by the lifetime hull warranties offered by the best builders. Some builders shape their hulls rather free form while with some others the aluminum sheets are forced into bends around an internal steel jig to shape the hull and then the panels are welded into place. A straight piece of aluminum sheet can flex under sufficient wave pressure. This flex, often referred to as oil-canning, can contribute to the noise often associated with aluminum hulls (topic covered below). By forcing the aluminum into an engineered bend around a jig, the material is put under tension which both increases its strength and takes away ‘oil-canning’. This is simple to see for yourself: take a business card gently between your thumb and forefinger and with your other forefinger poke it in the middle to see how easily it flexes. Now increase your grip pressure a bit so that the business card flexes slightly outwards, now poke it again, no flex, voila , you just engineered a stronger and quieter business card!.
Key attributes of aluminum are being both strong AND lightweight so in a nutshell a heavy gauge welded aluminum hull will be very strong in a lighter package than a comparably strong FG boat hull. End of story? Of course not!
We can all appreciate the safety, ruggedness, and long lifespan that a strong boat offers. But do we want light-strong or heavy-strong?
Light = less displacement = rides higher in the water. An advantage to this is we can get by with less horsepower and fuel to move the boat. Pretty much all will agree lower fuel consumption is very attractive. However these same attributes that make the boat easier to push tend to make the boat get ‘bounced around’ a bit more as wind and waves will have a greater effect on a lighter boat. In contrast to this the heavier FG boat all other things being equal will be more ‘look out waves I’m coming through’, just remember it will need more power and fuel to accomplish this.
Another popular attribute of aluminum is abrasion resistance, so if you want to beach your boat regularly, whether boat camping, unloading people and gear at the cabin, or going ashore for a hike or to get clams or oysters, the durable abrasion resistant aluminum is ideal.
Detractors of aluminum boats point out that they are noisy and in comparison they will tend to be more so than FG. Metal tends to transfer vibration, which can be heard as noise, while fiberglass absorbs vibration. We’ve all sat on the top deck of a BC Ferry and noticed that. In reality though both FG and aluminum pleasure craft hulls are foamed filled both for Coast Guard flotation and sound/temperature insulation. In an open boat ambient wind noise easily masks any hull noise but in my experience in a full cabin boat I will say hull noise is a bit more noticeable from an aluminum hull compared to a fiberglass hull.
Fiberglass boats will have the aesthetic advantage of having better visual looks and hull shapes. Since the material is molded, more advanced and attractive shapes can be made. Aluminum construction on the other hand is made from cutting, bending and welding large sheets of aluminum and various other aluminum angles and extrusions, thus an aluminum boat will tend to be a bit more basic/angular/industrial looking. Beauty is of course in the eye of the beholder.
So the answer is?? Of course there is no definitive answer which is why both types of boats remain so popular (remember those cement sailboats?!). If you want an attractive and sporty runabout for the lake, or a luxury cruiser, the aesthetics of fiberglass will probably push that boat to the top of your wish list. And if you own a pickup truck and value utility over flare I see a heavy gauge welded aluminum boat in your future.
SEE MORE BOAT BLOGS HERE